*This blog is part of a series you will find out that companies with high levels of performance visibility are well placed to deliver successful construction project. *
Measurable benefits of performance visibility
The Procore survey identified 3 measurable benefits of performance visibility
Money
survey respondents estimated that around five hours per week (c. 240 hours annually) were saved as a result of performance visibility.
Weighted to the relative sizes of the organizations and to measurable benefits of performance visibility the manpower costs involved, the results suggested average annual savings of £253,000 per business from addressing performance gaps in the UK and Ireland.
By contrast, those firms which had no visibility of performance estimated they were wasting an average of 3.5 hours per week, with average financial costs to each firm of around £265,626 a year due to poor performance.
Quality and Safety
were also improved through having performance visibility.
Respondents with Performance Visibility:
- 49% registered fewer defects,
- 48% reported better tracking of safety records, and
- 46% felt visibility supported their compliance with standards such as ISO 9001 / 45001.
Respondents without visibility of their performance globally felt they were hampered:
- 30% in managing risks,
- 25% in managing defects, and
- 23% in managing safety.
Monitor and Improve Project Performance with Lean.
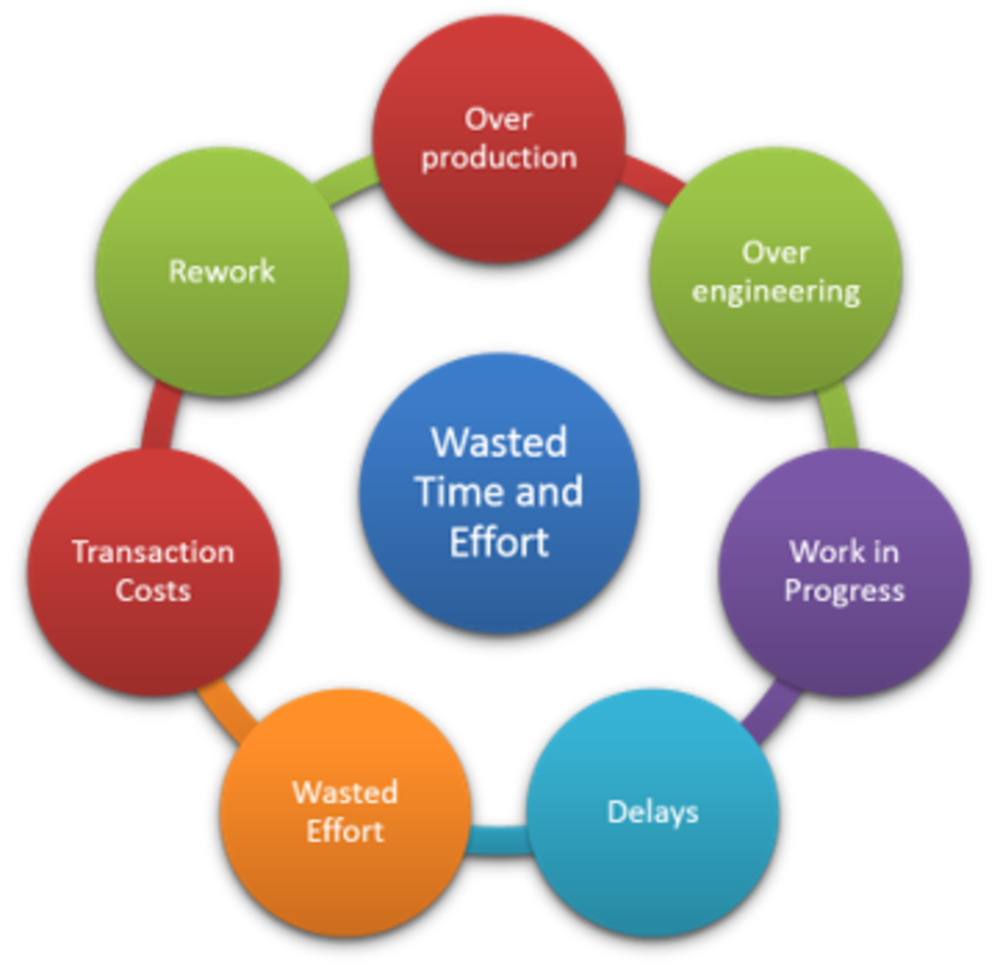
Driving Vision is SmartLeanBIM accredited, which means that we are always recommending to our clients the right BIM, at the right time and specifically for the right reason.
Lean thinking and Performance Measurement
The lean principles main benefits are:
- reduce nonvalue adding activities (waste),
- increase output value in accordance with clients’ requirements,
- reduce variability,
- reduce the cycle time,
- simplify the number of steps, parts, and linkages,
- increase output flexibility,
- increase process transparency,
- focus control on the complete process,
- build continuous improvement into the process,
- balance flow improvement with conversion improvement, and
- benchmark
What are the four categories of lean?
- philosophy: long term thinking
- process: eliminate waste
- people and partners: respect, challenge and grow them
- problem solving: continuous improvement and learning
What are the lean construction techniques?
- Parallel execution of various tasks by multidisciplinary teams with the goal of building a performant asset maximising functionality, improving quality, and increasing productivity. The success of lean construction is depending on the involvement of all participants in the early stages of the design.
- Completion of individual tasks by teamwork, ascertaining the stream of supply, design, and installation throughout production units using scheduling to determine the progression and rate of work.
- Team members share their views and what has been achieved, at the same time, discuss problems they are facing during the design and construction processes;
- Site warehouses allocate different materials and small tools to the workers.
- Satellite stores are situated on-site, where they get products from the site warehouse.
- Collection vehicle collects materials from preferred suppliers to the operational site using the concept of Just In Time.
- Plan health and safety into the project execution. These safety activities can generate limitations for scheduled tasks and that is why they should be embraced as a part of assignments.
- The fusion of quality management tools in lean construction is based on the change from conformance based quality to the quality at the source to help workers to follow planned controls instead of quality corrections,
- Identification of materials to accelerate repetitive processes and diminish the risk of selecting the wrong product, and
- Improve communication between decision-makers and workers through the cloud and mobile technologies to accelerate the process.
How to manage projects in lean construction?
- Determine client requirements and design to meet them,
- align the design to quality, schedule, and budget limits,
- manage the project by breaking it into small pieces, estimating duration and resource requirements for each piece, and then put the pieces in a logical order with the Critical Path Method,
- assign, or contract for each piece,
- give start notice and monitor each piece to assure it meets:
- safety,
- quality,
- schedule, and
- cost standards,
- act on negative variance from standards,
- coordinate using the master schedule and weekly meetings,
- manage cost reduction by productivity improvement,
- reduce the duration by speeding each piece or changing logic, and
- improve quality and safety with inspection and enforcement.
In conclusion
You should have the following objectives in place when implementing SmartLeanBIM:
- implement lean processes,
- identify the source of wastes classified under lean construction industry,
- understand the lean construction principles,
- evaluate the effectiveness of scheduling in teams to increase plan reliability,
- implement a continuous improvement programme in your organisation, and
- develop a model that identifies three critical elements:
- time spent on improvement,
- improvement of skills and mechanisms, and
- improvement of the perspective of the projects
Implementing BIM can be daunting, but Driving Vision is here to help you at the pace you are comfortable with. Get started by getting in touch now