This article is part of a blog series on Construction 4.0 technologies, exploring how they are changing the way we do business in the construction industry. The technological revolution in the construction industry is now called Construction 4.0. It is all about connectivity. The aim is to improve the way we do business in the Architects, Engineers, Construction, and Operations (AECO) industry.
Two major trends are talked about everywhere in the construction industry: Construction 4.0 and sustainability. They are normally discussed separately but are interdependent, so we explain in this article how they interlink.
Buildings are responsible for 37% of greenhouse gas emissions and for the economic and environmental sustainability of the AECO industry.
Green buildings benefit employees, bottom lines, and investors. The sustainability of the AECO industry is impacted by the various construction 4.0 technologies such as the Internet of Things (IoT) and drones.
Blockchain
The blockchain in construction takes control of supply chains and contracts in ways that were impossible ten years ago.
In the supply chain real-time tracking of materials and transactions with transparency, thanks to automated smart contracts helps to generate payments based on pre-defined milestones. The blockchain unchangeable data, allows to verify the goods provenance and quality. This gives stakeholders new control and visibility over construction.
Artificial intelligence
Artificial intelligence (AI) can enhance the job site safety from the design phase of construction by analyzing the data collected by drones about hazardous places on site and recommending solutions to navigate safely with autonomous vehicles to avoid potential accidents if humans were driving.
AI, analyzing data from previous projects, helps optimize resources, reduce costs by preventing overruns, and improve quality control through automated inspections.
Self-healing materials
Self-healing materials can integrate tiny capsules filled with healing agents that break open when the material is damaged, eradicating temporary scrape requirements and human inspection.
Releasing the agent into the crack generate a chemical reaction to fill the gap and solidify the damaged surfaces, "healing" the material. This process is initiated by stimulant heat, light, or the stress crack forming.
Scientific research
Scientists at the University of Exeter, in the United Kingdom, discovered that high carbon emissions can be lowered, productivity can be increased, and costs reduced if the industry adopted construction 4.0 technologies.
The framework they developed to increase the deployment of construction 4.0 technology addressed all negative impacts on sustainability.
The framework was evaluated in the United Arab Emirates where the construction industry is growing by 9% per year and is generating 75% of all solid waste in the country.
The researchers found that the usage of 4.0 technologies will increase by around 20% in all categories in the next five years.
They categorized the technologies in use as digitalization, automation, advanced manufacturing, integration and collaboration, and intelligent environment.
The break down provides a framework to understand and implement different aspects of the digital transformation within the construction industry. The model approach ensures optimizing processes, improving efficiency, and enhancing collaboration across all project stages byy identifying the primary functions of each technology group.
Breakdown of the categories:
Digitalization: convert physical data into digital formats through technologies like Building Information Modeling (BIM), sensors, and drones, to analyze and monitor the construction projects.
Automation: incorporates robotic systems and automated machines to perform repetitive tasks on construction sites, incresing productivity and deducing human error.
Advanced Manufacturing: Includes 3D printing and additive manufacturing,to customize construction components and implement efficient construction methods.
Integration and Collaboration: Connect all stakeholders through the project lifecycle using cloud-based platforms and collaborative tools, facilitating information sharing and decision-making.
Intelligent Environment: uses smart sensors and data analytics to monitor and optimize construction processes. This helps improve environmental conditions, energy usage, and safety measures.
We now look at how technologies can help the transformation and sustainability of construction over the next five years.
The Internet of Things (IoT)
This technology can keep track of materials and equipment, and continuously monitor dust, hazardous fumes, noise, vibrations, and motion detection.
The IoT was found to impact positively the environment thanks to real-time and accurate data collection. This led to improved analytics on material usage and waste.
Automation and advanced manufacturing technologies
Both automation and advanced manufacturing are the backbone of the industry. They help to reduce waste. They include robotics, drones, and 3D printing.
For example, it can reduce waste by allowing precise material cutting, optimizing resources, monitoring inventory, and minimizing errors. This leads to less scrap and more efficient materials use during the building process.
Integration and collaboration technologies
3D Building Information Modelling BIM and intelligent environment technologies such as machine learning, artificial intelligence, and smart materials, reduce paperwork.
Immersive Technologies (VR and AR) used in design and prefabrication help to minimize carbon emissions.
AR and VR help to reduce waste by providing virtual training platforms where employees can train without risks.
VR can optimize design processes and raise environmental awareness by engaging workers in virtual experiences leading to improved practices across various sites.
Energy-saving tools
Using AI to analyze water consumption, energy use, materials for environmentally friendly alternatives, and scheduling has proven useful in reducing the environmental impact and lowering the cost of construction projects.
Optimizing the operations of a building will help to reduce waste and energy by improving inspection and supervision.
Automating routine and administrative tasks helps to improve the safety of the building and its occupants.
The downside to improving sustainability using Construction 4.0 technologies will be the amount of computational power and the electronic waste generated to operate these technologies.
Fortunately, improving energy efficiency in data centers alleviates the negative impact of AI by minimizing the environmental footprint, optimizing power usage, and reducing waste within data centers.
It is also important to design more efficient AI models and select solutions that could offset the energy demands of AI.
Let us talk about sustainability
A report, from The Buildings-GSR, provides an annual review of the progress of the building and construction sector on a global scale. Last year’s edition highlighted the main factors as modest emissions reduction and limited sectoral progress, despite improvements, ,renewables, codes, and certifications.
You are probably already aware of the goal to prevent the temperature from increasing by more than 1.5%, from the United Nations.
They recommend halving emissions from the construction environment by 2030, operating all new buildings with a net zero in carbon by 2050, and avoiding any disruption from climate change.
The report is not optimistic about the sector reaching the 2050 decarbonization goals, however the More Science Based Targets initiative engaged 3,000 companies worldwide to commit to reducing CO2.
Futuristic building and sustainability
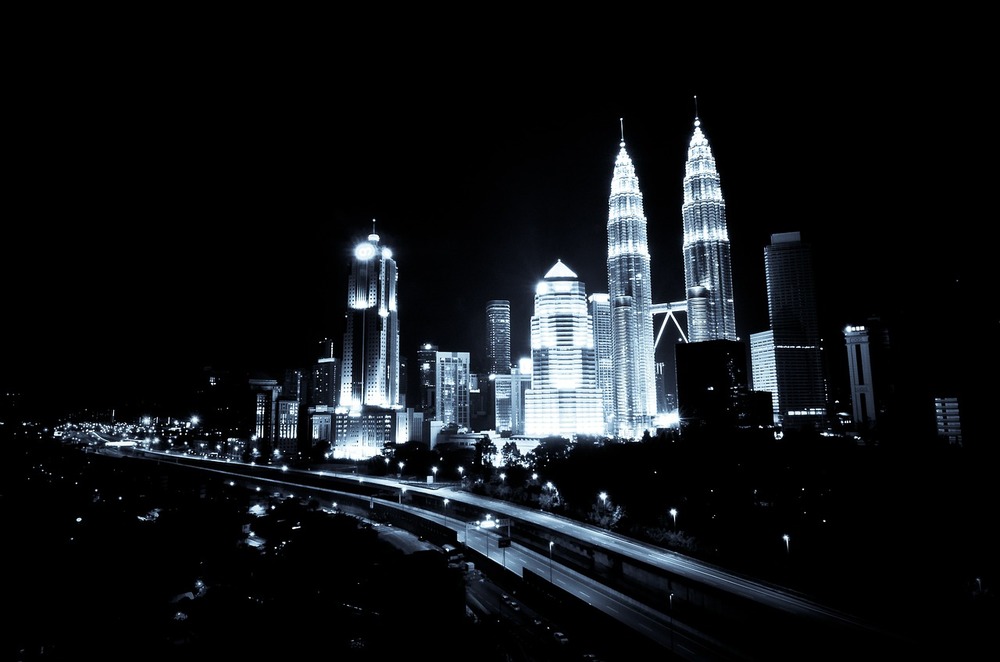
All is not as gloomy as the report shows. We see a lot of sustainability activities in the construction industry to make material steps to reduce its environmental impact.
The customers are becoming more sustainability-conscious, putting pressure on developers to lower the carbon footprint of new construction. Sustainability must be part of all new projects and construction processes.
Designers aim to reduce material waste from demolitions, switch to eco-friendly building materials, and choose locally sourced building products.
Clients are also pushing construction companies to provide sustainable, environmentally friendly practices.
How is construction becoming more sustainable?
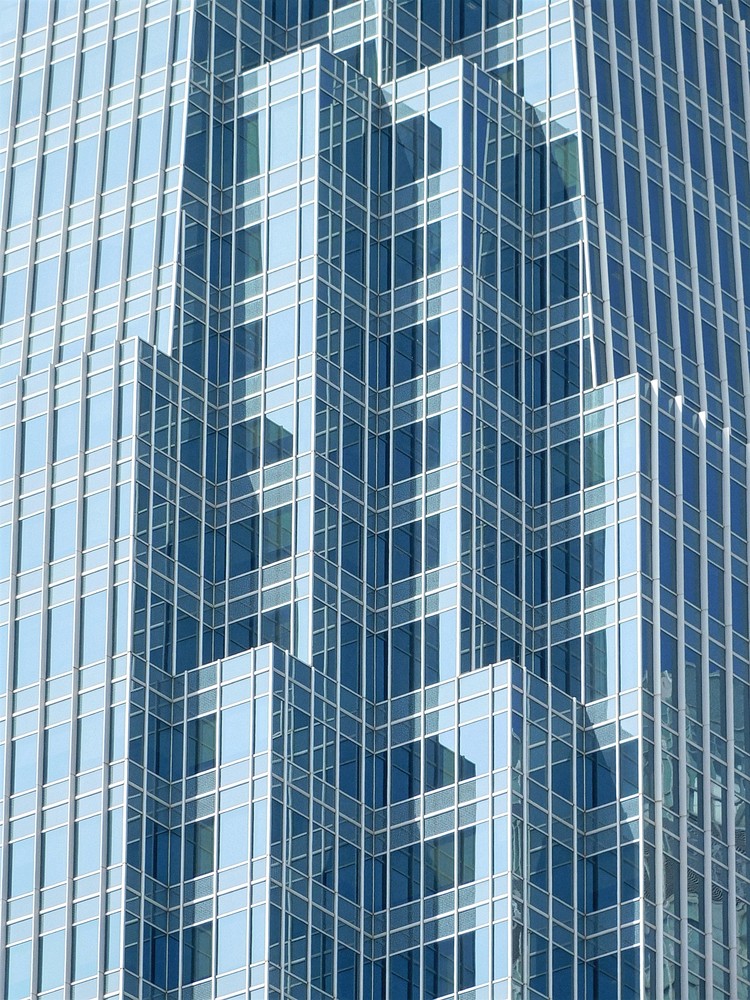
Let us look at how to cut emissions in construction and what drove sustainability in the last ten years.
Very often when you mention sustainability in the AECO industry people are exasperated as it is considered a banality in the sector. Is it ecological? Is it to minimize climate change?
What is the definition of sustainable constructions?
The UN World Commission on Environment and Development's definition of sustainability is:
Meeting our own needs without compromising the ability of future generations to meet their own needs.
Sustainable construction must use recyclable and renewable materials in all projects. It is important to reduce the impact on our environment by minimizing energy consumption and waste production
Sustainability covers the whole life cycle of a project
During the design phase, you should ensure that your construction will have a minimal environmental impact, over the project's lifespan.
The design should include objects and materials that impact the structure's environment like energy-efficient roof access, solar panels, or appropriate insulation.
What can you do to build sustainable constructions?
You can:
- use only natural resources that the planet can provide
- ensure not to pollute the air and water so you do not heat up our planet
- create processes and solutions that can last forever to keep our planet safe, beautiful, and enjoyable.
Digitalization drives sustainability
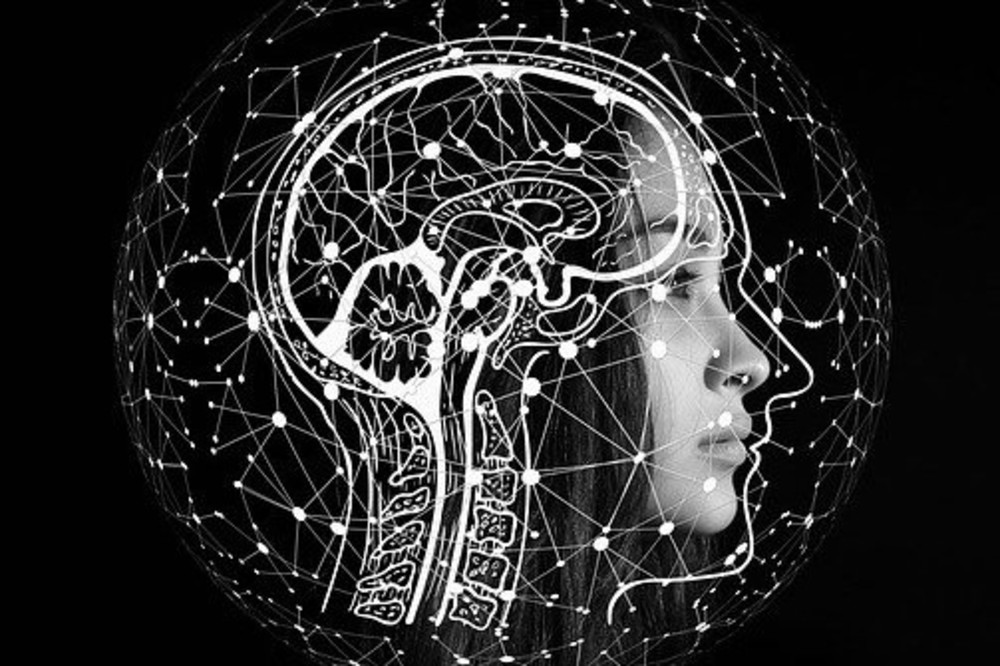
Eliminating waste
According to various sources of information we consulted in 2024, an estimated 3.6 billion tons of construction and demolition (C&D) waste was generated globally. A substantial portion was non-hazardous, of which 1.2 billion tons were recovered worldwide. Below are two examples of how to recover demolition waste.
3D printing used in construction is 70% faster, reduces materials used by 60% with no waste produced, and reduces the amount of water used in the building process.
Construction management software can help to understand and control your building process to optimize the number of materials you buy to ensure that you use, relocate, or reuse the excess material and keep track of your orders.
Streamlining processes
Digital tools can increase your efficiency by improving the quality of your building, delivering projects on time, and making your projects environmentally friendly.
BIM helps achieve sustainability goals by creating a virtual 3D model with data that allows you to complete energy-usage calculations and find building materials.
To achieve your sustainability targets, managing building life cycles helps reduce carbon footprints by developing efficient logistic plans, optimizing water and lighting consumption, reducing material requirements, and eliminating waste.
Collaborating with the contractors, and facility managers at the design stage, before construction starts, can help the designer to reduce the risk of costly reworks, and avoid waste of energy, water, and materials when the construction is in use.
Smart buildings
Buildings are called “smart” when they use technology to help manage resources and create a comfortable and safe space.
Smart buildings constructed with tools such as IoT sensors, building management systems, and artificial intelligence are good for the environment.
Green buildings obtain real-time data to understand the weather and optimize lighting and HVAC systems, reducing energy consumption and improving distribution system performance.
For example, water wastage can be avoided by monitoring the piping system with sensors. The system detects leaks early on by monitoring the flow rates. Unusual usage patterns are identified to optimize water pressure. Timely preventative measures are taken if the pattern goes wrong before water loss occurs.
Eco-friendly administrative processes
Cloud-based management software streamlines the construction process, saves resources, and reduces carbon emissions.
The system can also facilitate the electronic management of your documents, contracts, and invoices. It makes the process paperless and saves energy from printing. Sending documents electronically reduces emissions by avoiding sending them via traditional mail which requires transportation.
Flexibility
Sustainability is more than the climate and the environment. It is anticipating whatever the future can bring.
Remote working, following the pandemic, changed the way we operate.
By storing all information and data in the cloud, you can quickly find and access the right information from anywhere in the world and maintain effective communication.
BIM, immersive technologies, and electronic communication tools facilitate remote collaboration, avoiding inevitable carbon emissions if you had to travel to the site.
Investment and Return on Investment
The environmental benefits of sustainable building are obvious, but they cost money. How can we get a return on investment?
Green practices
Understanding the cost implications for green practices is important.
Analyzing the initial investment in sustainable construction compared to long-term savings and benefits may help the decision-making process about the viability and profitability of sustainability-friendly lifetime projects versus traditional ones.
By adding the financial support available through government incentives to reduce lifetime costs, the return on investment (ROI) may prove that sustainable construction practices are viable.
Recurring revenue
Another way to increase a company’s ROI in the construction industry is to get "recurring revenue".
Recurring revenue means creating a stream of income, when the construction is finished, from ongoing services like maintenance, repairs, or facility management contracts.
By offering ongoing services, construction companies can achieve more predictable revenue, improve cash flow, and increase profit margins rather than relying on one-off project income.
There are a few different types of recurring revenue contract, which we will explore below.
Maintenance contracts
Offering maintenance services for buildings or infrastructure billed annually with automatic renewal is a wonderful way to get predictable income.
Facility management services
Managing the day-to-day operations of a building after construction, on behalf of the owner, will get you a predictable and regular cash flow.
Repair services
When a developer has a multiple projects within a community, a great way to get recurring revenue would be to have a long-term contract agreement for repairs.
In conclusion
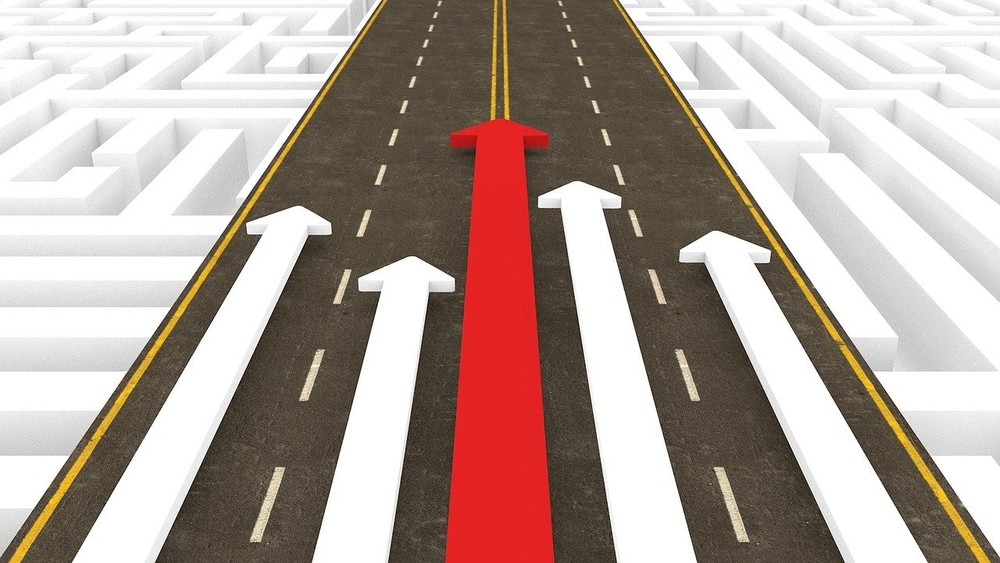
Management consulting firm McKinsey has launched the Net Zero Built Environment Council. The council includes members from across the construction industry. Its main goal is to examine how to eliminate greenhouse gas emissions from the built environment. Sub goals are to support stakeholders innovations by creating and commercializing "green" solutions.
The solutions include materials and technologies to enter ‘green’ markets, estimated to be worth $2 trillion, and promote methods of building that aids the decarbonization of the industry.
McKinsey's research found that half of all emissions across the built environment could be eliminated, projects could reduce by 20% the use of materials (i.e., cement and steel), and the industry could be decarbonized completely.
Connecting construction 4.0 and sustainability will force change and innovation.
Keeping pace with rapidly changing technologies makes you more agile to adapt to climate change. It builds a ring of innovation to achieve a better future.
It is time for you to embrace digital transformation and review your business model to make your business more sustainable, improve your decision-making process, and gain competitiveness.
Driving Vision's technology diagnostic looks at the best way to incorporate modern technology into your workflows and how to move your organization to the use of Construction 4.0 technologies so you can open new possibilities for your daily planning tasks.
The technology appraisal report will help you explore what investment is required to improve your projects’ productivity and collaboration and the ROI you can expect.
Implementing BIM can be daunting, but Driving Vision is here to help you at the pace you are comfortable with. Get started by getting in touch now